Lean Production or Industry 4.0? Let’s do Lean 4.0!
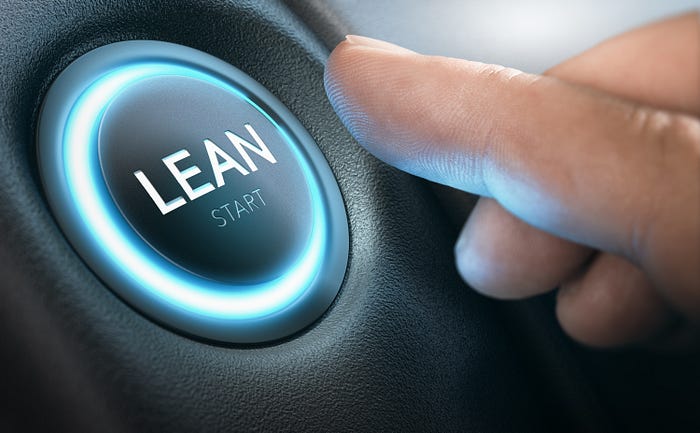
Lean 4.0 refers to the combination of Lean Manufacturing and Industry 4.0 tools.
Lean Manufacturing is a production philosophy developed by the Toyota Motor Corporation with the aim to reduce waste in the value chain in order to minimize lead time, costs and improve quality. With Lean Manufacturing, Toyota was able to gain a world leading position in the automotive industry.
Industry 4.0 aims to improve efficiency, transparency, flexibility leading to a scenario of mass personalization.
Both paradigms are promising to solve future challenges in manufacturing industries.
Mayr et al. (01) shows how Industry 4.0 tools can contribute to optimizing specific lean methods. A correlation matrix is shown in Figure 1:

Just-in-Time (JIT): it aims to deliver the right product at the right time, plce and quality in the right quantity for the right cost. Main Industry 4.0 tools to support JIT are:
- Automated Guided Vehicles (AGV): an automated guided vehicle (AGV) is a portable robot that follows markers or wires in the floor, or uses vision, magnets, or lasers for navigation. They are most often used in industrial applications to move materials around a manufacturing facility or warehouse. Application of the automatic guided vehicle broadened during the late 20th century.
- IoT: the Internet of Things (IoT) is the network of devices that contain electronics, software, actuators, and connectivity which allows these things to connect, interact and exchange data. IoT involves extending Internet connectivity beyond standard devices to any range of traditionally non-internet-enabled devices and everyday objects.
Heijunka: the goal is to level the production program to a constant rate so that the overproduction is reduced. Industry 4.0 tools are:
- Discrete Event Simulation (DES): this kind of simulation aims to predict the behaviour of the production system to analyze key metrics like OEE or bottlenecks. The DES simulation allows the optimization of the production system based on real data;
- Big Data Analytics: planning can be stabilized by using data history in combination with a better understanding of customer needs through an in-depth analysis of the market.
Kanban: the goal of Kanban is to retain a continuous material flow by maintaining a predefined stock level to guarantee an uninterrupted supply of material. Industry 4.0 tools are:
- Digital Twin: Digital Twin refers to a digital replica of physical assets, processes, systems and devices. It integrates artificial intelligence, machine learning and software analytics with spatial network graphs to create living digital simulation models that update and change as their physical counter parts change. Through simulation methods or virtual real time representation of physical objects, new Kanban loops can be planned with more foresight and seamlessly integrated into the existing production environment;
- IoT: a constant monitoring of work in process is possible.
Value Stream Mapping (VSM): it enhances the transparency of the material and information flow within the value creation chain to identify waste. I4.0 tools are:
- IoT: as for Kanban, sensors and auto-ID enables the instant localization of objects, big data and data analytics, making easier the creation of VSM;
- Machine Learning and data analytics support the creation of a value stream design and optimization. An optimized layout can be generated automatically once the requirements are known.
Total Productive Maintenance (TPM): it is a system of maintaining and improving the integrity of production and quality systems through the machines, equipment, processes and employees and focuses on keeping all equipment in top working condition to avoid breakdowns and delays in manufacturing processes. I4.0 tools to support TPM are:
- Virtual Reality (VR) and Augmented Reality (AR): “Augmented reality (AR) and Virtual Reality (VR) can be considered two sides of the same coin. They both aim to extend the sensorial environment of an individual by mediating reality through technology. The former relies on an alternative setting to experience, while the latter improves existent elements with additional layers of meaning”. (02)
These technologies facilitate training as well as maintenance instructions. Moreover, by displaying virtual elements operators can be guided remotely.
- With Machine Learning and Data Analytics, correlation between condition parameters and the probability of defaults can be analyzed.
Single Minute Exchange of Die (SMED): it aims to reduce the downtime and cost caused by setup processes. The one-piece-flow approach is pushing to minimize as much as reasonably practical the set-up time. I4.0 tools are:
- AR and VR: VR can be used to train people to perform set up operations on order to shorten the learning curve. AR can support the worker during set up operations by displaying work instructions on a headset;
- Additive Manufacturing: it is any of various processes in which material is joined or solidified under computer control to create a three-dimensional object, with material being added together (such as liquid molecules or powder grains being fused together). When AM can be used to produce final product, the set-up time can be reduced to a minimum.
Visual Management (VM): the purpose of VM is to enhance transparency by transferring targets, standards and specifications into a visual representation. Part of VM is 5S, which is a systematic approach to organize the workplace and improve clarity through keeping the workspace clean and arranging tools properly. Tools to support VM and 5S are:
- IoT & AR: they help to assist carrying out 5S more efficiently. RFID ensures the identification and localization of objects which reduces search time. By means of markers like warning signs, AR may also be used for zoning, which means the identification of determined working areas;
- HMI: Human Machine Interface (HMI) is basically a device, most of the time a touch-screen, which interfaces the machine and the operator. HMI like tablets, smartphones, head-mounted displays and smart watches me be used to show real-time notifications to users;
Poka-Yoke: it describes mechanisms that help operators to avoid mistakes. I4.0 tools are:
- IoT and Auto-ID: they ensure the correct identification and assignment, or the correct picking;
- Artificial Intelligence and Machine Learning: machines can automatically adapt processes to ensure optimal product quality;
- AR: as stated before, AR can support the worker during set up operations by displaying work instructions on a headset.
Conclusion
In this post, a quick overview on Lean 4.0 has been described. Lean and Industry 4.0 are complimentary approaches that can provide significant benefits to manufacturing organizations in terms of waste reduction quality and efficiency.
If you want to stay update to Innovation and Manufacturing topics, please follow me or subscribe to my newsletter!
References
01 — Mayr A. et al, Lean 4.0 — A conceptual conjunction of lean management and Industry 4.0, 51st CIRP Conference on Manufacturing Systems, Procedia CIRP 72 (2018), pp 622–628, page 624
02 — Gandolfi E, Handbook of Research on K-12 Online and Blended Learning (2nd ed.), Publisher: ETC Press, Editors: Kennedy, K, Ferdig, R.E., pp.545–561